Share
Pin
Tweet
Send
Share
Send
Ale doświadczenie rzemieślników pokazuje, że nawet nie znając branży tokarskiej, można wykonać mechaniczny tasak z improwizowanych materiałów, dostosowując go do miejsca, objętości pracy i danych antropometrycznych.

Będzie potrzebować
Zasadniczo prawie wszystkie materiały i zespoły do montażu mechanicznego tasaka można usunąć ze starych samochodów, sprzętu gospodarstwa domowego i znaleźć na wysypiskach śmieci. Ale nie zaszkodzi wiedzieć, ile ta lub tamta „rzecz” jest w sklepie, ile silnik będzie kosztował ze starej pralki, o co zwróci się do tokarza o pracę itp.
Co więc powinniśmy zaopatrzyć, jeśli zdecydujemy się na mechaniczny tasak:
- okrągła stal walcowana (drewno okrągłe);
- taśma maskująca;
- blacha o różnych grubościach;
- rura profilowa około 14 m;
- koło zamachowe z GAZ-53;
- śruby, nakrętki, podkładki;
- silnik z kołem pasowym i pasem;
- farba i pędzel;
- tasak ślimakowy marchewkowy.
Z narzędzi i wyposażenia, które musimy mieć pod ręką:
- młynek z dyskami;
- plazmoreza;
- pilnik do metalu;
- sprzęt spawalniczy;
- imadło i zaciski;
- wiertarka z wiertłami.
Produkcja sęków i detali splittera
Naprawiamy okrągłe drewno w imadle i zaznaczamy miejsca cięcia taśmą maskującą, aby zapewnić szybkość i łatwość zapewnienia pożądanej dokładności.

Zgodnie z oznaczeniami wycinamy półwyrób wałka łuparki do drewna za pomocą szlifierki i tarczy tnącej 180 mm.
Powierzchnię grubej blachy oznaczamy dwoma dyskami o różnych rozmiarach, ale tymi samymi otworami środkowymi.
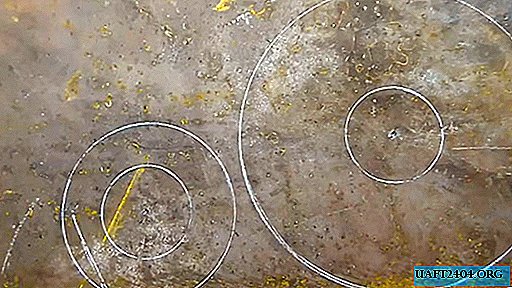
Bardziej wygodne i dokładne jest cięcie ich za pomocą przecinarki plazmowej, w wyniku czego ilość późniejszej obróbki jest zminimalizowana.
Dyski doprowadzamy do pożądanego rozmiaru za pomocą pilnika i młynka, a aby nie usuwać nadmiaru metalu, wklejamy na boczne powierzchnie dokładne wzory taśmy lub papieru.

Główną uwagę przy obróbce tarcz poświęca się środkowym otworom: półwyrób wału musi swobodnie wchodzić do nich, ale jednocześnie szczeliny powinny być minimalne.
Ta operacja jest jedną z kluczowych: spawamy duży dysk dokładnie pod kątem 90 stopni do okrągłego drewna. Dlatego starannie przeprowadzamy spawanie, stale sprawdzając kąt między częściami, aby nie prowadziły, i używamy kwadratów magnetycznych. Czyścimy spoiny.
Drugi pierścień jest łatwiejszy do zainstalowania. Wystarczy mocno go docisnąć i przymocować do pierwszej tarczy zaciskami i spawać w tej pozycji.


Teraz tokarz będzie pracował na przedmiocie: szlifuje przednią podporę, która jest przyspawana do mniejszego pierścienia, szlifuje okrągłe powierzchnie na wymiar i wykonuje szereg rowków pierścieniowych pod paskiem napędowym.
Z rury profilowej wycinamy przedmioty o wymaganym rozmiarze i wymaganej ilości, z których spawamy nie tylko pulpit, ale podstawę do montażu również zamontowanych jednostek.


Oddzielnie spawamy ramę pomocniczą do ramy głównej pod blatem, do której silnik elektryczny zostanie przymocowany i wyregulowany.

Z metalowej płyty o grubości 6 mm wycinamy szlifierkę dwie symetryczne części, które zespawane razem i przymocowane do blatu będą rodzajem ogranicznika ostrza na łuparce do drewna.

Ponieważ obciążenie naszego urządzenia będzie się stale zmieniać, nie można tego zrobić bez koła zamachowego. W naszym przypadku koło zamachowe GAZ-53 o średnicy zewnętrznej 372 mm, otworze do lądowania 40 mm i masie prawie 16 kg okazało się najbardziej odpowiednie pod względem wielkości i masy.

Usuwamy koło koronowe z tej części i oczyszczamy je z długotrwałego tłustego zabrudzenia za pomocą młotka, końcówki wkrętaka i młynka z dyszami.

Wyważamy statycznie wał i koło zamachowe, przykręcając je do siebie śrubami i nakrętkami. Z powodu braku wyważarki wymyślamy ją przy użyciu wyłącznie dostępnej gotówki.


Aby to zrobić, tymczasowo umieść równolegle dwa rogi na ramie stołu i delikatnie je chwyć. Korzystając z poziomu, zapewniamy maksymalną możliwą płaskość narożników i nakładamy na nich wałek z kołem zamachowym.

Obróć koło zamachowe i monitoruj moment zatrzymania. Jeśli jest na niej niewyważona masa, to przed zatrzymaniem lekko się cofnie. Ponadto nadwyżka masy będzie w najniższym punkcie. Zaznaczamy to miejsce i wiercimy otwór, usuwając w ten sposób nadmiar masy.

Wyważanie zostanie uznane za zakończone, gdy wał i koło zamachowe nie przetoczą się przed zatrzymaniem.
Dla bezpieczeństwa z resztek rury profilowej i blachy wykonujemy ochronną osłonę na kole zamachowym i gotujemy blat stołu.


Łączymy ze sobą dwie symetryczne części pod kątem, wewnątrz mamy przekładkę i przyspawamy powstały zespół do blatu.

Wszystkie węzły i części są wykonane, więc zacznij je malować zwykłym pędzlem.
Szacowane koszty
Oszacujmy, ile kosztuje nas domowy rozdzielacz:
- koło zamachowe - 1200 rubli;
- rura profilowa 14 m - 1200 rubli;
- silnik z myjki (730 W, 8 tysięcy obr./min) - 530 rubli;
- „marchewka” (średnica podstawy - 70 mm, wysokość - 250 mm) - 1300 rubli;
- dwa 206 łożysk w obudowie - 600 rubli;
- praca tokarza - 1650 rubli.;
- sprzęt i pasek napędowy - 530 rubli.
W sumie okazuje się, że około 7 tysięcy rubli. To 3 razy mniej niż najtańszy rozdzielacz fabryczny.

Montaż węzłów i detale rozdzielacza
Mocno przymocuj koło zamachowe do wału, załóż pasek, zespoły łożyskowe i przymocuj zespół do ramy.
Instalujemy i mocujemy „marchewkę” na końcu wału za pomocą dwóch specjalnych kołków.


Napinamy pasek, przekręcając śrubę przeznaczoną do tego celu, która opiera się o podporę, popycha silnik i pociąga pasek.
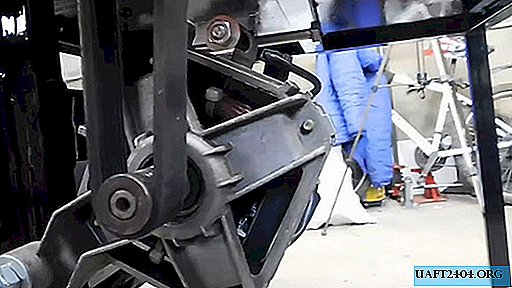

Elektryk składa się z przewodu zasilającego, przełącznika i regulatora napięcia ze szlifierki. System połączeń jest dość standardowy.


Podczas uruchamiania obecność regulatora eliminuje szarpanie i zapewnia płynny zestaw obrotów za pomocą koła zamachowego. Jest to bardzo ważne, ponieważ pasek nie wsuwa się w rowki, co oznacza, że będzie trwał dłużej.
Ponadto, dzięki regulatorowi napięcia, możesz zmienić moc, co bez obciążenia natychmiast prowadzi do zwiększenia prędkości.
Instalujemy osłonę na kole zamachowym, aby chronić siebie i osoby w pobliżu przed obrażeniami, jeśli koło zamachowe nagle wyleci z wału lub pęknie.

Test łuparki do drewna w biznesie
Najpierw spróbuj podzielić mały kawałek planszy. Dzięki niej nasze domowe poradzi sobie bez wysiłku. To samo dzieje się z suchymi polanami, które były przechowywane pod baldachimem: całkowicie bez stresu łuparka do drewna prostuje dość masywny konopie.

Jeśli nagle „marchewka” utknie w kłodzie, to wyłączając zasilanie za pomocą klucza, obracając wał za plecami, bez żadnych problemów uwalniamy narzędzie robocze z kłody, w której utknął.

Nawet ta niewielka praktyka pokazała, że mocowanie marchewki na wale musi być zagłębione, aby nie przeszkadzało w rąbaniu drewna, a stół powinien znajdować się na całkowicie poziomej powierzchni. Zapobiegnie to nawet niewielkim drganiom podczas pracy rozdzielacza.
Nie można również pracować na tym urządzeniu w rękawiczkach i rękawicach z jednym palcem, a rękawy ubrania nie powinny być zbyt długie i bez sznurówek, pasków i innych wiszących elementów, aby nie skręcały się „marchewki” i nie raniły rąk.

Share
Pin
Tweet
Send
Share
Send